Introduction
Cocoa is a widely consumed commodity globally, with its primary application being the production of chocolate. The increasing demand for chocolate products has spurred the interest of entrepreneurs and investors in establishing cocoa processing factories. However, understanding the cost implications involved in setting up a cocoa processing plant is crucial for planning and budgeting purposes. In this article, we will delve into the various factors that contribute to the cost of cocoa processing factory.
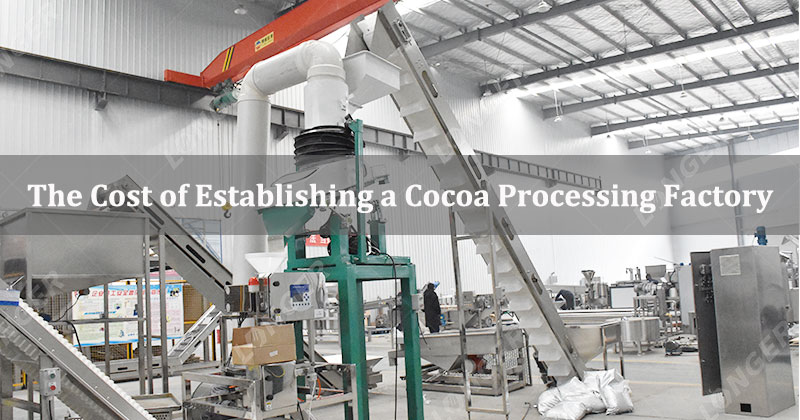
1. Plant Capacity and Scale
The scale and capacity of the cocoa processing factory play a significant role in determining the overall cost. The plant’s capacity is usually measured in terms of cocoa bean processing capacity per annum, such as 10,000 metric tons or 20,000 metric tons. Higher capacity plants require larger infrastructure, machinery, and utilities, resulting in higher initial capital investments.
2. Infrastructure and Building Costs
The cost of acquiring or constructing the infrastructure for the cocoa processing factory is a substantial expenditure. Factors such as land acquisition, site preparation, building construction, utilities (water, electricity, gas), waste management systems, and safety compliance contribute to the overall infrastructure cost. The location of the plant, local construction costs, and regulatory requirements influence these expenses.
3. Machinery and Equipment
Cocoa processing plants require a range of specialized machinery and equipment for efficient operations. This cocoa powder processing machine includes cleaning and sorting equipment, roasting machines, winnowing machines, grinding mills, hydraulic presses, conching machines, and packaging equipment. The cost of machinery depends on factors such as capacity, quality, automation, and technological sophistication. Opting for newer, more advanced machinery can increase the initial investment but may offer long-term cost savings through improved efficiency and productivity.
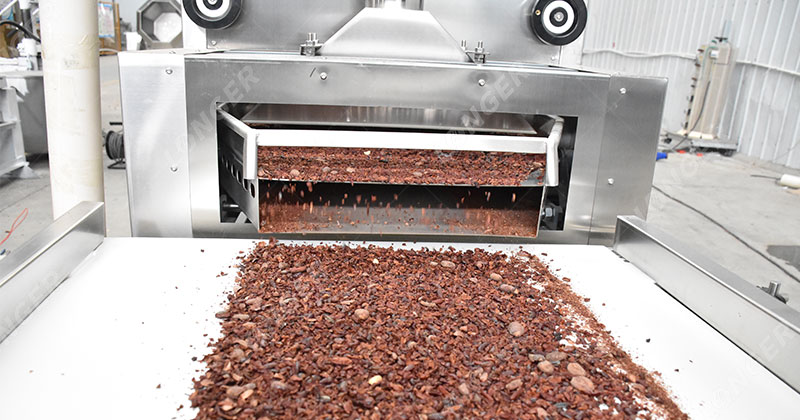
4. Utilities and Services
Utilities such as water, electricity, and gas are essential for the operation of a cocoa processing plant. Costs associated with utility connections, consumption, and ongoing maintenance must be considered. Additionally, services such as waste management, pest control, security, and insurance contribute to the operational expenses of the plant.
5. Labor and Workforce
The cost of labor depends on various factors, including the plant’s location, labor market conditions, and local regulations. Skilled labor is required for the operation and maintenance of machinery, quality control, packaging, and administrative tasks. Training programs and ongoing staff development may also be necessary to ensure optimal performance and productivity.
6. Regulatory Compliance
Complying with regulatory standards and obtaining necessary licenses and permits can involve costs. These include environmental regulations, food safety standards, workplace safety requirements, and certifications such as Fair Trade or organic certifications. It is crucial to allocate budgetary resources for regulatory compliance to avoid legal and operational complications.
7. Research and Development
Investing in research and development (R&D) is vital for continuous improvement, innovation, and meeting changing consumer preferences. Allocating funds for R&D activities such as product development, process optimization, and quality enhancement allows the plant to stay competitive and adapt to market demands.
8. Contingency and Miscellaneous Expenses
It is essential to allocate a contingency budget to account for unforeseen expenses or project delays. Miscellaneous expenses may include legal fees, consultancy fees, project management costs, initial raw material inventory, marketing and branding expenses, and other incidental costs that may arise during the plant setup phase.
Conclusion
Setting up a cocoa processing plant requires careful financial planning and consideration of various cost factors. Infrastructure and building costs, machinery and equipment, utilities, labor, regulatory compliance, research and development, and contingency expenses all contribute to the overall cost. Conducting a detailed feasibility study, obtaining multiple quotes from suppliers, and seeking professional guidance can help in accurately estimating the cost of establishing a cocoa processing plant. By comprehensively analyzing the costs involved, entrepreneurs and investors can make informed decisions.
If you need cocoa processing machinery or more information, welcome to contact us.
Email: [email protected]
WhatsApp/Mobile: +8615515597212